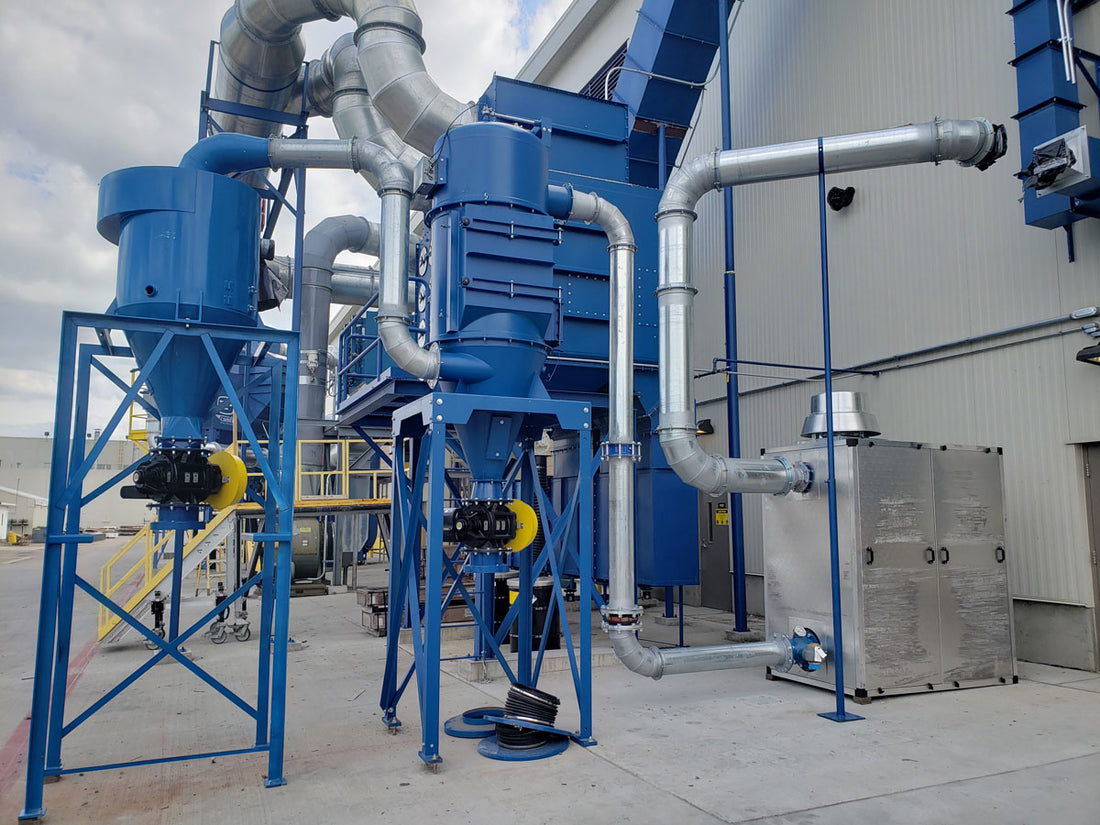
The Hidden Costs of Poor Filter Management for HVAC and Chillers: How It Impacts Your Bottom Lin
Share
The Hidden Costs of Poor Filter Management for HVAC and Chillers: How It Impacts Your Bottom Line
Effective HVAC and chiller system maintenance is essential for businesses, but filter management often falls through the cracks. While it might seem like a minor operational detail, neglecting timely filter replacements can snowball into significant financial consequences. From energy inefficiencies to equipment downtime and compliance risks, poor filter management directly affects a corporation’s bottom line. Here’s how—and the numbers to prove it.
1. Increased Energy Costs
Dirty or clogged filters force HVAC and chiller systems to work harder to maintain airflow and temperature control. This strain increases energy consumption, driving up utility costs.
- Energy Impact: According to the U.S. Department of Energy, clogged filters can increase energy usage by 15-20% for HVAC systems.
-
Financial Example:
- A medium-sized office building with an annual energy bill of $100,000 for HVAC can incur an extra $15,000-$20,000 per year due to dirty filters.
- Multiply this by multiple buildings, and costs quickly escalate for corporations with large portfolios.
2. Equipment Wear and Tear
Filters act as the first line of defense, trapping dirt, debris, and contaminants that can otherwise damage system components. Poor filter maintenance accelerates wear on fans, coils, and compressors.
-
Repair Costs:
- Compressor replacements for commercial HVAC systems can range from $2,500 to $15,000.
- Regularly replacing filters, which typically cost $50 to $200 each, can prevent such expensive repairs.
- Long-Term Impact: Premature equipment failure caused by neglected filters may shorten the lifespan of HVAC or chiller units by 30-40%, forcing corporations to replace systems earlier than planned. A new commercial HVAC system can cost $5,000 to $50,000+ depending on size.
3. Decreased Productivity and Employee Well-being
Poor air quality caused by neglected filters can lead to uncomfortable working conditions, employee illness, and decreased productivity.
-
Health Costs:
- Dirty filters result in poor indoor air quality, increasing allergens, dust, and pathogens. This contributes to 40% of building-related illnesses, according to the EPA.
- For companies with 100 employees and an average annual salary of $50,000, just a 1% productivity loss due to poor air quality can cost $50,000 annually.
- Turnover and Morale: Employees dissatisfied with working conditions are more likely to seek employment elsewhere, leading to increased turnover and hiring costs.
4. Regulatory Non-Compliance
Certain industries, such as healthcare, food processing, and manufacturing, must meet strict air quality and operational standards. Poor filter management can lead to non-compliance fines and reputational damage.
-
Compliance Costs:
- Fines for failing to meet air quality standards can range from $5,000 to $25,000 per violation.
- In healthcare settings, improper filter maintenance can jeopardize certifications and contracts, leading to potential revenue loss.
5. Downtime and Business Interruptions
Neglected filters can cause HVAC and chiller systems to fail unexpectedly, leading to costly downtime. This is especially critical for temperature-sensitive industries like food processing or high-occupancy buildings.
-
Downtime Costs:
- In manufacturing, HVAC failure causing production halts can cost $10,000 to $50,000 per hour in lost output.
- For businesses like hotels or retail stores, customer dissatisfaction due to uncomfortable conditions can result in revenue loss and damaged reputations.
6. The Multiplier Effect: Scaling Costs for Multi-Site Corporations
For corporations managing multiple facilities, these costs multiply significantly. For example:
-
Corporation with 20 buildings:
- Extra energy costs due to clogged filters: $300,000 annually (assuming $15,000 per building).
- Premature equipment replacements for 5 HVAC systems: $150,000-$250,000.
- Productivity loss across 1,000 employees: $500,000 annually.
How Proper Filter Management Saves Money
-
Energy Efficiency Gains:
- Replacing filters regularly can reduce HVAC energy consumption by 10-15%, translating to thousands of dollars in savings per facility annually.
-
Prolonged Equipment Lifespan:
- With proper filter maintenance, HVAC systems can last 20-25 years, compared to 12-15 years with poor management. Avoiding premature replacements saves tens of thousands per system.
-
Improved Productivity:
- Enhanced air quality can boost employee productivity by 1-5%, adding substantial value, especially in large organizations.
-
Compliance Assurance:
- Regular maintenance prevents costly fines and protects certifications in regulated industries.
-
Avoiding Emergency Repairs:
- Preventative maintenance minimizes unexpected breakdowns, reducing downtime and avoiding costly emergency service fees.
Final Thoughts: Turn a Cost into an Investment
Managing HVAC and chiller filters proactively isn’t just about avoiding problems; it’s about protecting your bottom line. Regular filter replacements ensure energy efficiency, extend equipment life, improve employee well-being, and prevent compliance risks. For corporations, the investment in a proper filter management program can save hundreds of thousands of dollars annually.
By partnering with a reliable supplier that offers tailored solutions, scheduling tools, and high-quality filters, businesses can eliminate these challenges and turn routine maintenance into a strategic advantage.