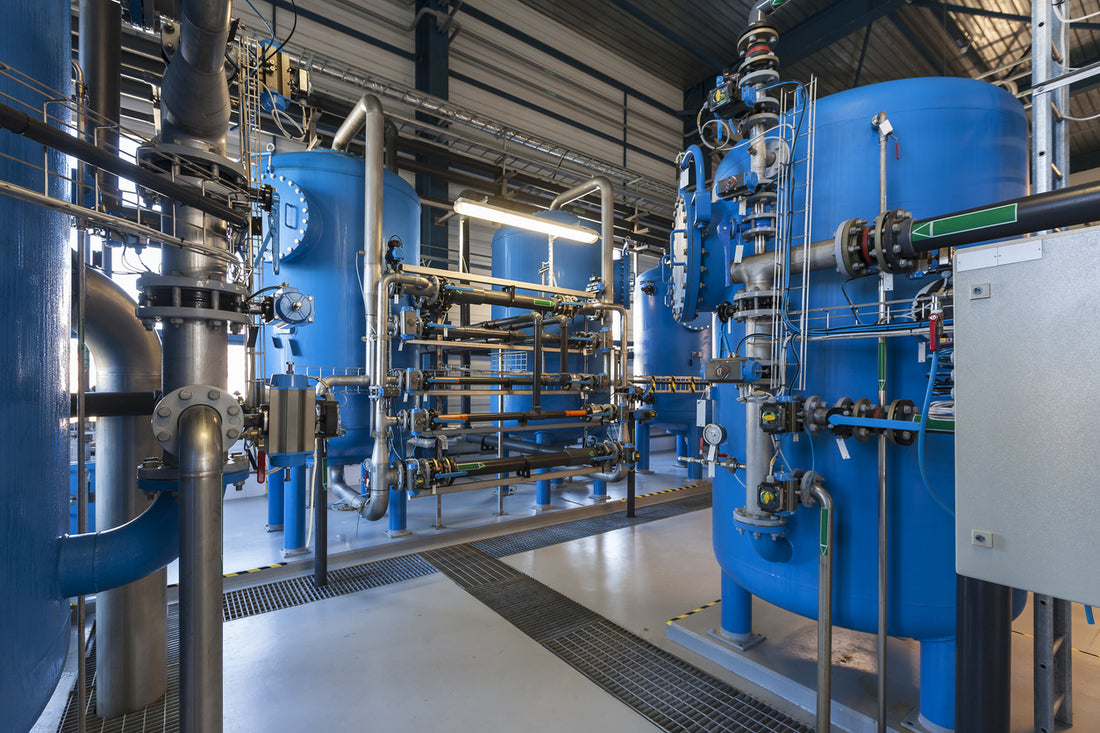
The High Stakes of Water Filtration in Manufacturing and Industrial Operations
Share
The High Stakes of Water Filtration in Manufacturing and Industrial Operations
In manufacturing and industrial operations, water is a critical resource used for cooling, cleaning, and even as a direct component in production processes. Yet, many facilities overlook the importance of proper water filtration systems, leading to costly equipment damage, production delays, and compliance issues. Poor water quality doesn’t just affect efficiency—it directly impacts the bottom line.
In this blog, we’ll explore the unique challenges faced by manufacturing and industrial facilities, the high stakes of neglecting water filtration, and how partnering with the right vendor can transform operations.
The Role of Water in Manufacturing and Industrial Operations
Water serves multiple purposes in industrial settings:
- Cooling: Used in chillers, heat exchangers, and cooling towers to regulate temperatures in machinery and processes.
- Cleaning: Essential for washing components, equipment, and final products to maintain quality standards.
- Process Integration: Used as a key ingredient in products like chemicals, electronics, or pharmaceuticals, requiring ultrapure water for specific applications.
- Steam Production: Boilers rely on clean water to generate steam for various manufacturing processes.
The High Stakes of Poor Water Filtration in Industry
-
Equipment Damage and Downtime
- Scale Build-Up: Hard water minerals like calcium and magnesium accumulate on equipment surfaces, leading to inefficiencies and increased energy use. For example, scale can reduce boiler efficiency by 10-15%, costing facilities thousands of dollars annually in additional energy consumption.
- Corrosion: Impurities in water, such as chlorides or sulfates, accelerate the corrosion of pipes, heat exchangers, and machinery. Repairs or replacements can cost anywhere from $10,000 to $100,000 per system.
- Unexpected Downtime: A single day of downtime in a manufacturing plant can result in losses ranging from $10,000 to $50,000, depending on production scale and product type.
-
Product Quality Issues
- Contamination: Poor water quality introduces contaminants into products, leading to defects, recalls, or rejections from clients. For example, trace impurities in water used for pharmaceutical manufacturing can render an entire batch unsafe, costing hundreds of thousands of dollars.
- Process Inconsistencies: Variations in water quality can disrupt chemical reactions or alter product specifications, jeopardizing quality control.
-
Compliance Violations
- Regulatory Fines: Many industries must adhere to strict water quality and wastewater discharge standards set by organizations like the EPA. Non-compliance can result in fines exceeding $25,000 per violation or even production shutdowns.
- Environmental Impact: Facilities discharging untreated water risk harming local ecosystems, leading to reputational damage and legal consequences.
-
Increased Maintenance Costs
- Frequent Repairs: Poor water quality accelerates wear and tear on equipment, requiring more frequent repairs and servicing.
- Replacement Cycles: Equipment subjected to unfiltered water often fails prematurely, reducing the lifecycle of critical systems.
Challenges in Industrial Water Filtration
-
High Volume Requirements
- Manufacturing facilities often consume hundreds of thousands of gallons of water daily, requiring filtration systems capable of handling large-scale operations without sacrificing efficiency.
-
Varied Contaminants
- Industrial water sources may contain sediment, heavy metals, oils, and biological contaminants, all requiring specialized filtration technologies.
-
Custom Needs for Specialized Applications
- Industries like microelectronics or pharmaceuticals require ultrapure water, while others, like food processing, prioritize removing organic matter and pathogens.
-
Aging Infrastructure
- Many facilities operate with outdated plumbing or filtration systems that can no longer meet modern demands, leading to inefficiencies and increased costs.
Solutions: Advanced Water Filtration Systems for Industry
-
Reverse Osmosis (RO) Systems
- Removes up to 99% of dissolved solids, heavy metals, and contaminants, making it ideal for cooling systems and production processes requiring high-purity water.
-
Water Softeners
- Reduces hard water minerals to prevent scale build-up in boilers, heat exchangers, and other critical equipment. This can extend equipment life by 20-30% and reduce maintenance costs.
-
Filtration for Cooling Towers
- Specialized filters designed to remove biological growth, scale-causing minerals, and sediment, improving energy efficiency and reducing the need for chemical treatments.
-
Carbon and Sediment Filters
- Removes organic matter, chlorine, and other impurities that can corrode equipment or contaminate products.
-
Custom Industrial Filtration Solutions
- Tailored systems that address specific contaminants and operational needs, ensuring optimal performance for unique processes.
Benefits of Partnering with the Right Vendor
-
Expertise in Industrial Applications
- The right vendor understands the complexities of industrial water use and provides systems designed to meet specific operational and regulatory needs.
-
Reliability and Support
- Ongoing maintenance, timely filter replacements, and rapid troubleshooting minimize downtime and ensure consistent performance.
-
Cost Savings
- Advanced filtration systems reduce energy costs, extend equipment life, and prevent expensive repairs or replacements. For example, a properly maintained system can cut energy use by 10-20%, saving tens of thousands of dollars annually.
-
Compliance Assurance
- Vendors knowledgeable about regulatory requirements ensure facilities stay compliant, avoiding fines and protecting reputations.
Final Thoughts
In manufacturing and industrial operations, water filtration is not just an operational detail—it’s a strategic investment. Poor water quality can lead to equipment failures, product contamination, regulatory violations, and skyrocketing costs, putting profitability and reputation at risk.
By implementing advanced water filtration systems and partnering with an experienced vendor, facilities can ensure smooth operations, protect their bottom line, and maintain the high standards their industries demand. Don’t let poor water quality disrupt your business—take control with the right filtration solutions today.